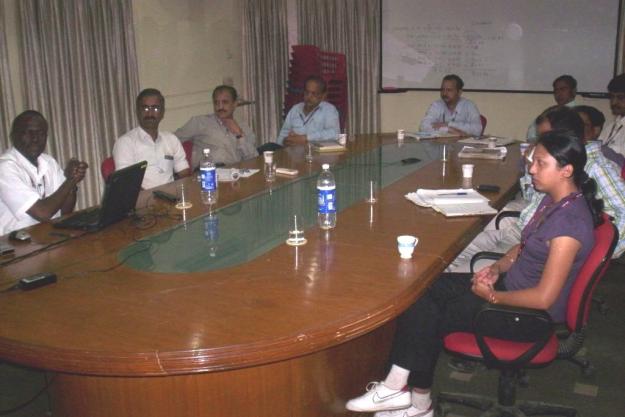
Two participants from Africa at United Phosphorus Limited in Ankleshwar, India, as part of the OPCW 2008 Associate Programme training course.
By: Mr S. K. Kothari, General Manager (Works)
Mr Stephan Lawrence Okuni, an analytical officer in the Government Analytical Laboratory of Uganda, and Ms Sanjana Devi Kisoona, a forensic scientist in the Forensic Science Laboratory of Mauritius, were asked to go to United Phosphorus Limited in Ankleshwar, India, as part of the OPCW 2008 Associate Programme training course. The period of their stay in India was from 25 August to 12 September 2008.
United Phosphorus Limited is among the largest generic agro-chemical and responsible care company in the world. It was involved with formulating a training programme for candidates sponsored by the OPCW. The course also included project work on improving process safety in a chemical plant.
The Associates worked closely with the Safety Manager and with the plant operating team in order to gain a wider understanding of manufacturing operations and associated safety requirements in relation to the chemical industry. Mr Okuni and Ms Kisoona were provided information about the conceptual design, operational systems, supply chains, and safety, health, and environment (SHE) aspects relevant to the chemical industry.
In addition, the Associates learnt about safety systems, such as HAZOP [1], the material handling system, MSDS [2], and associated trip interlocks [3] that form part of the safety process in regard to the handling of chemicals. The Associates prepared their project report in collaboration with the relevant personnel, and also made an in-house presentation on their topic. At Ankleshwar, both participants received in-depth information about both the theoretical and practical aspects of the manufacturing process.
[1] HAZOP stands for “hazardous operations”, and consists of a systematic examination of processes and operations to identify potential risks to personnel or equipment, or to efficient operations. The concept of HAZOP was defined by Imperial Chemical Industries (ICI) in 1963.
[2] Process safety: a blend of engineering and management skills focused on preventing catastrophic accidents, particularly explosions, fires, toxic releases (associated with the use of chemicals and petroleum products).
[3] “Interlocks” usually refer to protective systems for various types of storage systems, i.e. pressurised, refrigerated, and atmospheric storage.